USBL-1 Laboratory Blending System
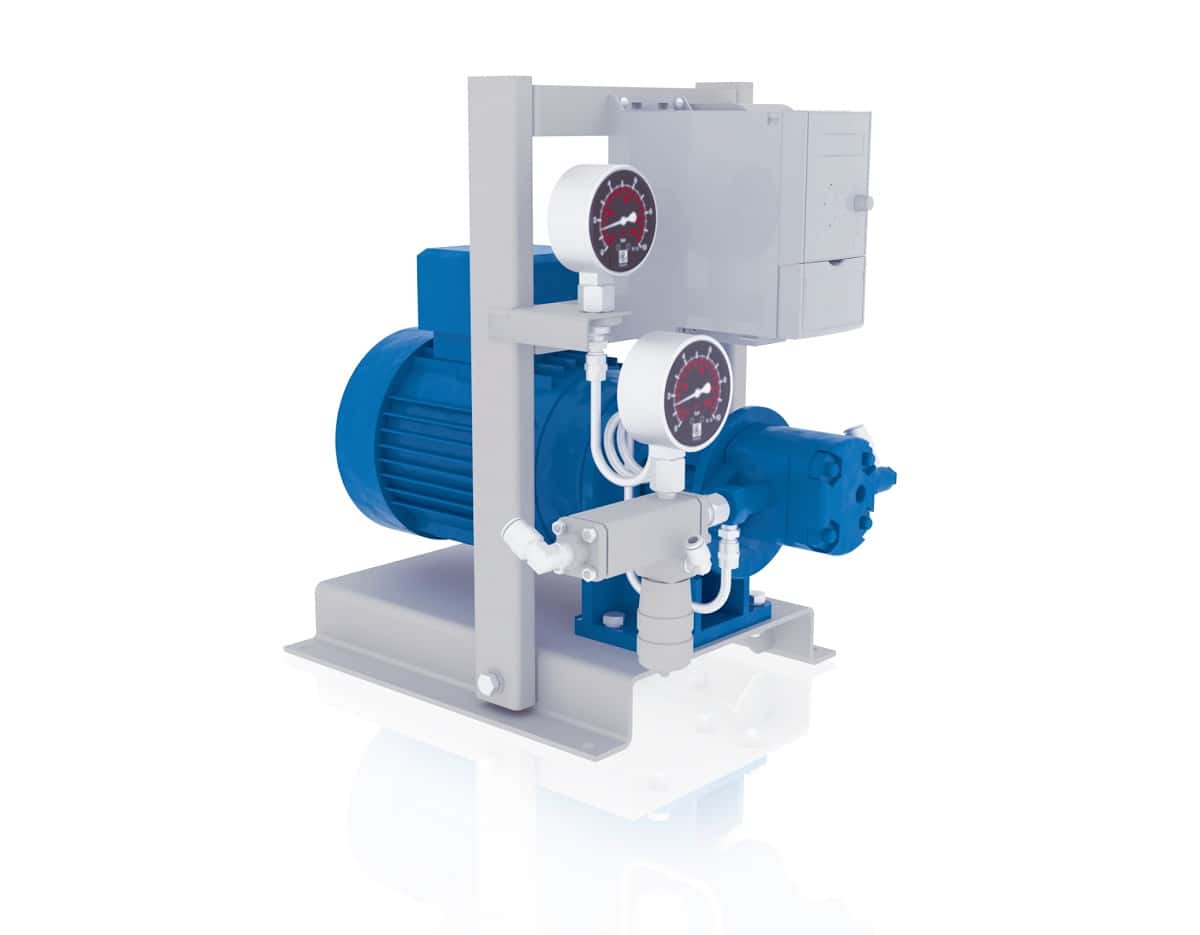
USBL-1
The high-speed laboratory blending unit USBL-1 is designed for accurate and high-quality blending of liquids of two components of oil...
-
Advantages
- it can be used by research institutions and laboratories;
- produces samples of mixed liquids for laboratory testing;
- helps in testing the effectiveness of various additives and optimizing mixing formulas.
The high-speed laboratory blending unit USBL-1 is designed for accurate and high-quality blending of liquids of two components of oil products, even in small volumes. This ensures high quality and consistency of the final product.
This unit can be used in laboratories at oil refineries. Its main purpose is to accurately and quickly mix 2 components, allowing specialists to accurately determine the right ratio of components to achieve the optimal result.
The resulting sample can then be directly used for detailed laboratory analysis to ensure compliance with all quality standards.