CLM-100.2 Colloid Mill
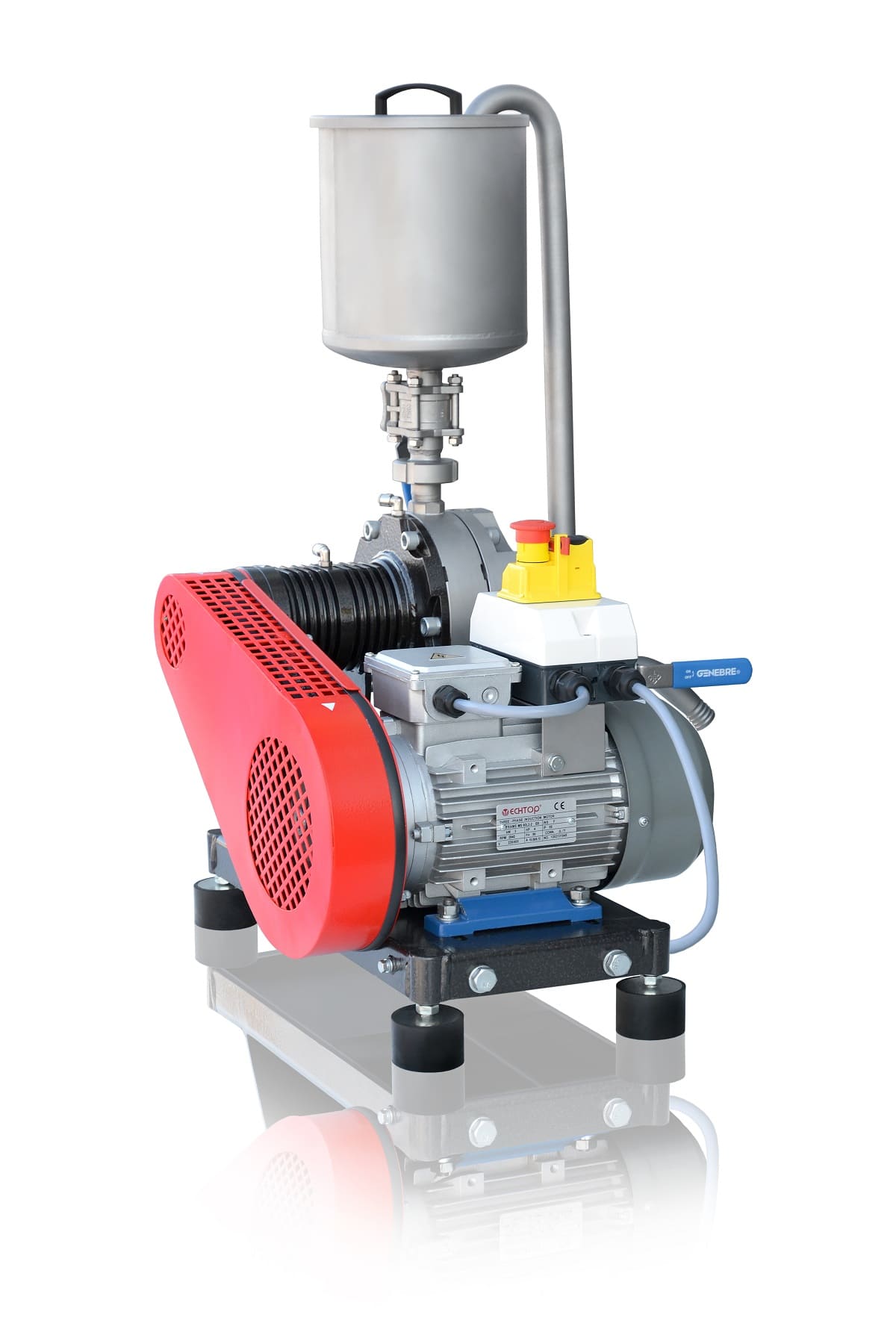
CLM-100.2
-
Advantages
- the mill can be used to develop new product formulations;
- the mill handles various types of products;
- compact size;
- design components of the mill wetted portion are made of stainless, chemical resistant steel;
- the mill can have the rotor/stator tooling of various types and the number of operating stages (rings) depending on the type of processed substance and required impact (nozzle, chamber, cone for milling, cone for viscous products);
- the tools can be collapsible, or made from a solid workpiece and various grades of steel depending on the intended purpose of the mill;
- the mill can be operated both indoors and in sheltered outdoor space.
CLM-100.2 colloid mill is designed for homogenization and emulsification of liquid products in a laboratory environment.
The mill can be used to prepare, dissolve, and process many products in various industries, as well as to obtain thick slurries of high shear stresses.
Principle of operation
The principle of operation of CLM-100.2 colloid mill is based on a rotor/stator system diagram. A rotor and a stator consist of concentric tool rings (cutters, knives) with special configurations of grooves and (or) holes that ensure the optimal mode of mechanical impact on processed product.
In working position, the tool rings of the rotor (moving tool) and the stator (stationary tool) enter coaxially against each other and rotate in a contact-free manner at a high relative speed (up to 50 m/s). Contact-free rotation is ensured by technological axial and radial gaps.
The processed product enters the operating chamber of the mill housing through the axial bore of the stator, is run through the rotor/stator system and discharged in the radial direction (product outlet).
When passing through the rotor/stator system, the product is influenced by complex hydrodynamic processes associated with changes in shear stresses, shear forces, and flow velocity. Chemical reactions occur faster due to increased contact surfaces of chemical agents. As a result, intensive dispersion, emulsification, homogenization, grinding, and pulverization of the processed product are achieved.