AVS-100 Mixing Machine. Vortex Layer Device
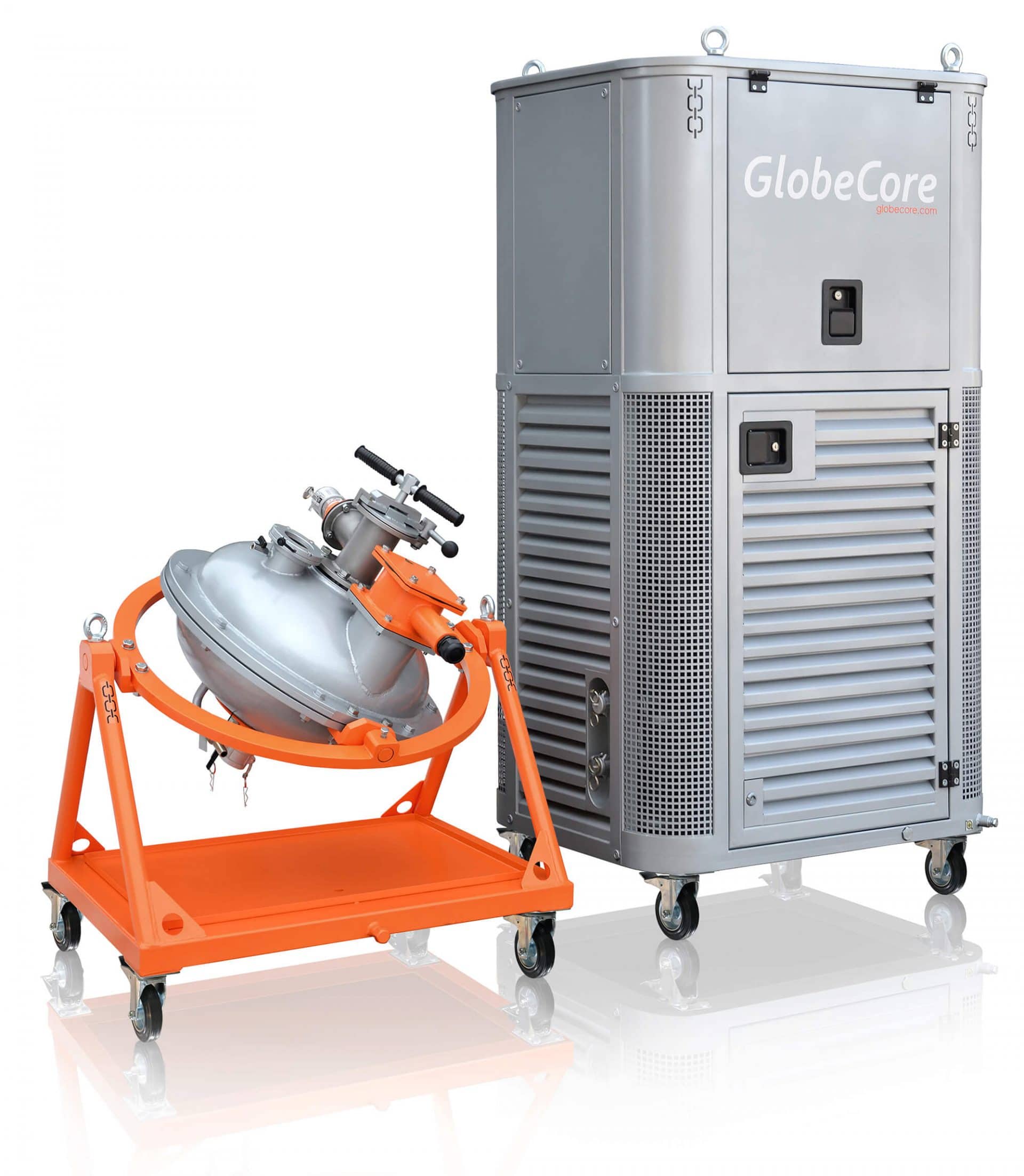
AVS-100
GlobeCore is the world’s only high-tech company for production of operating vortex layer devices with real applications in the industrial...
-
Advantages
- simultaneous pulverization, mixing and activation of processed media;
- super-fine pulverization;
- process intensification. Retention times measured in fractions of a second;
- reduced power consumption;
- raw material economy;
- simple to retrofit into existing processing lines.
Request Price
Fig. 1. Electromagnetic vortex system: 1 – protective bushing; 2 – inductor of rotating electromagnetic field; 3 – inductor body; 4 – non-magnetic material work operating chamber; 5 – ferromagnetic elements |
Figure 2. A photo of vortex layer (1000 frame per second camera) | Fig. 3. The chamber of AVS for liquid phase processes: 1 – chamber; 2 – bush; 3– strainer; |
Fig. 4. AVS chamber with knives: 1 – knoves; 2 – chamber; 3– mesh filter; 4 – bush. |
Fig. 5. AVS chamber with tubes: 1 – chamber; 2 – mesh; 3 – bush; 4 – tubes; 5 – filter tube |
Fig. 6. AVS chamber with rotor: 1 – chamber; 2– bronze bushings (lubricated and cooled by the processed liquid); 3 – lid; 4 – rotor |
The AVS-100 with ferromagnetic elements is designed to intensify6An intensification is an increase in strength or magnitude (or intensity). various physical and chemical processes.
The units can be efficiently used for
- production of multicomponent emulsions7An emulsion is a mixture of two or more liquids that are normally immiscible (unmixable or unblendable). and suspensions8A suspension is a heterogeneous mixture that contains solid particles sufficiently large for sedimentation.;
- acceleration of production of finely dispersed9A dispersion is a system in which distributed particles of one material are dispersed in a continuous phase of another material. The two phases may be in the same or different states of matter. mixtures;
- activation10Activation generally refers to the process whereby something is prepared or excited for a subsequent reaction. of materials both in dry form and dispersed in water;
- leading to improved properties of resin and decreased vulcanizing time;
- for complete purification of industrial waste water11Wastewater (or waste water) is any water that has been affected by human use. from phenol, formaldehyde, heavy metals12Heavy metals are generally defined as metals with relatively high densities, atomic weights, or atomic numbers., arsenic, cyanides;
- acceleration of heat treatment,
- production of protein material from yeast cells;
- improvement of microbiological stability of food products and activation of yeast in bread baking;
- improvement of crude products and finished products from meat and fish;
- intensification of extraction13An extract is a substance made by extracting a part of a raw material, often by using a solvent. processes, including production of broth, juice, pectin etc.
- production of suspensions and emulsion of increased microbiological safety in food production without the used of staibilizers and increase of product output.
The rotating electromagnetic field causes the ferromagnetic elements in the active zone to move and create the so called “vortex layer”
AVS Systems could be used as:
Error: Failed to load filter data