USB-1 Fuel oil blending system
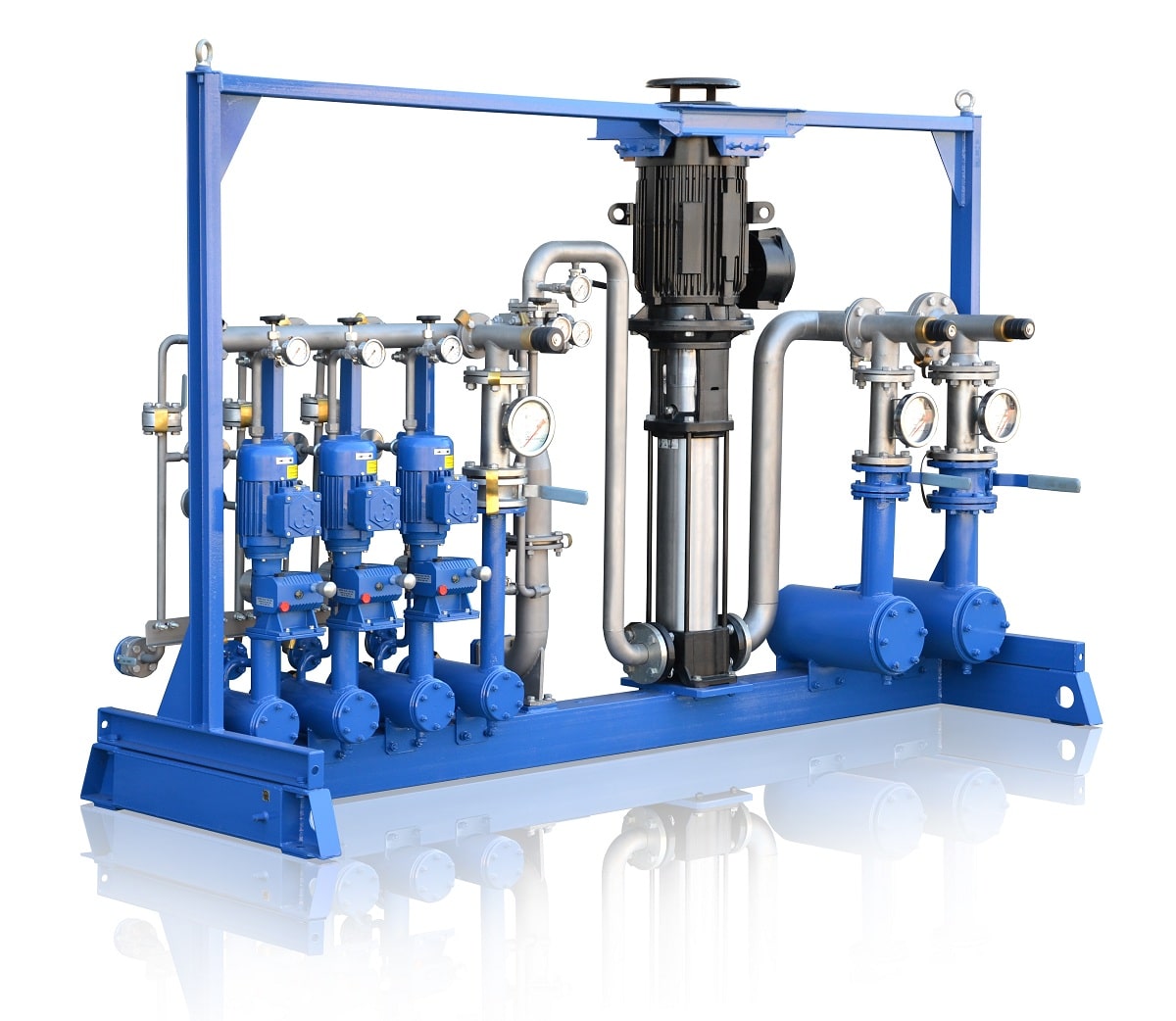
USB-1
-
Advantages
- Compounding of blended fuels (gasoline, diesel) to reduce light fraction consumption;
- Power savings: the unit is equipped with one motor and one pump only;
- Reduction of viscosity, hydrogen sulfide, chlorine salts, ash and paraffin content in crude oil;
- Compounding of oil improves the quality of straight run fractions: reduction of sulfur content and improvement of octane number of gasoline, reduction of sulfur and cloud point of diesel fuel;
- Improvement of fraction quality reduces the costs of finishing treatment;
- All equipment certified by the corresponding international bodies.
- Low power consumption;
- High energy of cavitation;
- Cheap energy conversion into cavitation;
- Simple operation;
- Advanced controls;
- Available with any production capacity;
- Combination of several processes;
- Easy integration;
- Low metal costs;
- Simple adjustment for optimal performance.
USB unit advantages for oil refineries:
The compounding units increase light fraction yield. It is also possible to equalize several types of oil for refinery stability. The unit saves electric energy and time and increases quality of all oil products.
Advantages of hydrodynamic acoustic cavitation units:
GlobeCore develops and manufactures inline continuous USB-1 biodiesel1Biodiesel refers to a vegetable oil- or animal fat-based diesel fuel consisting of long-chain alkyl (methyl, ethyl, or propyl) esters blending2A blending is the process of mixing. systems, designed for compounding of fuels and any other liquid ingredients, including bioethanol3Bioethanol is an alcohol produced from organic biomass such as sugar, wheat or maize, and represents over 80% of global biofuel production. and liquids of vegetable origin.
These biodiesel blending systems come in several types, can be designed stationary or mobile (installed on trailers, in vans or on railroad flatbed cars etc). The client specifies the type ingredients and the final product for customization of the unit. The blending units be used to produce any fuel blens: summer diesel4Diesel fuel in general is any liquid fuel used in diesel engines, whose fuel ignition takes place, without any spark, as a result of compression of the inlet air mixture and then injection of fuel., winter diesel, arctic diesel, Euro-45European emission standards define the acceptable limits for exhaust emissions of new vehicles sold in the European Union and EEA member states (Euro-1, Euro-2, Euro-3, Euro-4, Euro-5, Euro-6). high-octane gasoline6A Gasoline is a colorless petroleum-derived flammable liquid that is used primarily as a fuel in spark-ignited internal combustion engines., Euro-5 fuel etc.
The main purpose of these systems is intensification7An intensification is an increase in strength or magnitude (or intensity). of dispersion8A dispersion is a system in which distributed particles of one material are dispersed in a continuous phase of another material., homogenization9Homogenization or homogenisation is any of several processes used to make a mixture of two mutually non-soluble liquids the same throughout. This is achieved by turning one of the liquids into a state consisting of extremely small particles distributed uniformly throughout the other liquid. and emulsification10An emulsion is a mixture of two or more liquids that are normally immiscible (unmixable or unblendable). and blending of seemingly immiscible liquids and suspensions. The final product is a steady mix, which remains stable for a long time.
Hydrodynamic continuous mixers:
This type of equipment includes compounders, cavitators11Cavitation is a phenomenon in which rapid changes of pressure in a liquid lead to the formation of small vapor-filled cavities, in places where the pressure is relatively low., blenders, dispersers, homogenizers etc.
We develop and manufacture custom equipment of this types, tailored to the individual needs of the client, with attention to the finest details of the process, and supplied to the client directly from the manufacturer.
Our USB-1 blending systems are delivered worldwide and are operated today in more than 53 countries, where hundreds of facilities operate GlobeCore blending units. The units work in any climatic zones and climatic conditions from -65 to +55 degrees Celsius.
Our compounding12A compound is a substance formed when two or more chemical elements are chemically bonded together. systems come with the capacity of 5 to 600 t/hour and the possibility of compounding 2 to 7 components in any proportion with the possibility to fine tune the ratios.
Each unit is developed and manufactured for the specific client, according to the requirements of the customer; the equipment is integrated into existing processes, or can be used as part of entirely new process facilities.
Our compounding units are used for:
- Blended fuel production
- Gasoline blending
- Blending of diesel + biodiesel
- Blending of gasoline + bioethanol
- Winter diesel fuel production
- Arctic diesel fuel production
- Increased efficiency of hydrodesulphurization by pre-processing of distillates13Distillation is the process of separating the components or substances from a liquid mixture by using selective boiling and condensation. for the production of modern environmentally friendly fuels
- Detergent production
- Shampoo production
- Lubricant cooling liquid production, made by mixing the base liquid additives.
FUEL OIL BLENDING SYSTEM
Our company develops various innovative, energy-saving equipment and technologies. Our products are available under GlobeCore trademark (Oldenburg, Germany).
The main purpose of our products is intensification14An intensification is an increase in strength or magnitude (or intensity). of dispersion, homogenization and emulsification of various substances, many of which seem to be immiscible. The end product is a stable finely dispersed mixture with a long storage life and a very low tendency to separate.
Some of the hydrodynamic mixing15The hydrodynamic mixer is designed for mixing drip liquids in the production process. units are compounders, cavitators, blenders, dispersers, homogenizers and other types of equipment.
Our engineers have been perfecting and developing blending systems since the 1960s; thousands of such units have been produced.
We take custom orders: to suit client needs, we manufacture blending systems according to the clients individual requirements with careful consideration of the technology process.
Our units are used in more than 70 countries now. Below is a description of the processes the units are used for:
Light and dark petrochemical material production
This includes production of various materials from oil (high quality 95 octane gasoline, bio-gasoline, Euro-compliant diesel fuel, light heating oil16Heating oil is a low viscosity, liquid petroleum product used as a fuel oil for furnaces or boilers in buildings., dark heating oil, heavy oil according to Euro-4 standards, paints, biodiesel etc).
Our units and solutions are designed for:
- Compounding of multi-component mixes to produce motor fuel, biogasoline and biodiesel, to improve octane number17An octane rating, or octane number, is a standard measure of the performance of an engine or aviation fuel. The higher the octane number, the more compression the fuel can withstand before detonating (igniting). of low-octane fuel etc;
- Production of multi-component combustion18Combustion is burning a fuel in oxygen, which gives out heat energy and is called an exothermic reaction. fuels: water-fuel emulsions, water-oil emulsions for boilers, blending of various liquids and mixing additives to liquid fuels;
- Production and preparation of diesel fuel, production of winter and arctic fuel by mixing in anti-gel and anti-freezing additives, economizing of heating fuel, water-oil emulsions, heavy fuel and coking industry products.
Our USB-1 units have been supplied to over 53 countries, to hundreds of industrial facilities, where they are operated in all climate zones with temperatures from -65 to +55oC.
All USB-1 unit types are very simple to operate, easy to install, have a small footprint and come complete with full documentation and installation assistance service.
The blended gasoline production units are built for 5 to 600 tons per hour capacity for 2 to 7 ingredients.
Each unit is designed for a specific client, according to client requirements. The equipment can easily be integrated into existing processing equipment.
Compounding
Compounding means mixing two or more fuel, oil or other ingredients to achieve specific product parameters.
Processing of oil and petrochemical products in the USB-1 units occurs under highly intensive hydrodynamic and cavitation conditions, created by the sharp drop of pressure in the hydrodynamic (also known as trans-sonic) jet mixer with powerful physical influence on the processed fluid.
The method and technology of treatment in a subsonic flow is capable to change the structure of the fluid, increases light fraction yield, improves such properties as viscosity, sulfur and paraffin composition, accelerates additive mixing when making blended gasoline, water-fuel emulsion and mixes, oils, greases and other fluids.
The unit is designed for petrochemical facilities, filling stations and refineries. Besides, the technology and the equipment is widely used in over 400 industries, such as paint production, food production, mining, metallurgy, perfumery etc.
The compounding units are used for:
- Blended fuel production;
- Blended gasoline production;
- Blending diesel with biodiesel;
- Blending gasoline and bioethanol;
- Production of winter diesel fuel;
- Production of arctic diesel fuel;
- Improvement of hydro sulfur removal by pretreatment of distillates in production of modern environmentally clean fuel;
- Production of various surfactants;
- Detergent production;
- Production of lubrication materials, coolants etc, by blending a base liquid with additives.
Our compounding units have a range of advantages, and first of all, it is a complete unit easily integrated into any production cycle.
Results of USB-1 unit implementation
The USB-1 units are operated by many heating facilities successfully, as illustrated by the results of commissioning and operational tests of boilers of varying capacity, which use heavy heating oil and water-oil emulsion for fuel, with water content 8-20% (boilers tested in similar operating modes):
Parameter changes when burning fuel-water emulsion fuel Savings of heating oil depend on combustion equipment (boilers, burners) and original fuel oil parameters. Saving range is 8 to 20%. The amount of emissions to the atmosphere drops by 70-75%, soot emissions decrease significantly Bottom water disposal is not required, bottom water is distributed uniformly in the fuel oil. Boiler reliability improves, since loss of flame due caused by water in the fuel is eliminated entirely. Uniformity of combustion is improved. The amount of solid deposits on the walls of the boiler and gas ducts is reduced.
Parameter | Changes when burning fuel-water emulsion fuel |
Straight heating oil consumption | Savings of heating oil depend on combustion equipment (boilers, burners) and original fuel oil parameters. Saving range is 8 to 20%. |
Atmospheric emissions | The amount of emissions to the atmosphere drops by 70-75%, soot emissions decrease significantly |
Bottom water disposal | Not required, bottom water is distributed uniformly in the fuel oil. |
Boiler reliability | Reliability improves, since loss of flame due caused by water in the fuel is eliminated entirely. Uniformity of combustion is improved. |
Boiler wear | The amount of solid deposits on the walls of the boiler and gas ducts is reduced. |