A transformer is a complex system the reliable operation of which depends on many components. Among these components, a special role is assigned to transformer oil that performs a heat-removing and insulating function. In this article, we will discuss how and why the condition of oil deteriorates, what effect water and oxygen have on oil, and what technologies are better to use for drying and oil degassing the transformer oils.
How and why does the condition of oil deteriorate?
When a transformer operates, the oil is affected by various negative factors. These include:
- electric field;
- heat;
- -atmospheric oxygen;
- water;
- mechanical impurities;
- structural materials (metals).
Some factors such as electric field and high temperature are objective; it means they always exist regardless of the intent of transformer developers or energy companies. Some causes of other factors can be limited (water, air). But it is impossible to prevent the exposure of oil to harmful factors, because they are a catalyst of changes in oil and result from chemical reactions in a transformer. Gas bubbles may become a place where partial discharges evolve; water reduces the dielectric strength of oil, and when migrating into solid insulation, it contributes to degradation thereof.
Oil aging occurs over time, and acidic products of hydrocarbon oxidation are formed therein. These products settle on the insulation, the transformer tank walls, in the cooling system, and sludge is formed. The oil becomes more viscous and much worse at removing the heat from the transformer heating parts. As affected by highly concentrated products of hydrocarbon oxidation, decomposition of cellulose in a transformer occurs. The risk of emergencies considerably increases.
Insulating oil must be properly and timely maintained in order to ensure transformer service life extension. Owing to that, the transformer service life will be 50–70 years long.
What is required to improve the condition of oil?
When the condition of transformer oil deteriorates, the oil is processed in order to improve its characteristics. The main indicator of oil aging is the acid number. As long as this parameter does not exceed 0.5 mg KOH/g, purification is performed to improve the condition of oil.
Transformer oil purification is a broad definition which can be understood to mean a set of different procedures with each allowing you to get rid of a certain type of impurities.
These procedures include:
- oil filtration – to remove mechanical impurities;
- oil degassing – to remove gases;
- transformer oil drying – to remove free or dissolved water.
Furthermore, vacuumizing is used when supplying dry and degassed oil to high-voltage transformers. This procedure is necessary for preventing the ingress of water and gases into oil in the course of filling.
Besides, the overall status of insulation system is improved by transformer insulation drying in vacuum ovens. It is applied to remove water from the windings insulation.
An increase in the acid number to 1 m KOH/g is indicative of oil aging. In this case, transformer oil change or regeneration is performed. Oil properties can be reclaimed if the composition of useful hydrocarbons is preserved by removing the oxidation and aging products. If the composition of oil has altered to a great extent and cannot be reclaimed, the oil must be changed.
First, let us discuss preventive methods for protecting a transformer against water and gas formation, and next — the oil drying and degassing method.
Oil purification by GlobeCore CMM unit in the working transformer
Methods for protecting a transformer against exposure to water and gases
There are several approaches to protecting transformers against the effects of water and gases. Small transformers are manufactured in a sealed design. It places additional demands on the tank strength, because a fragile tank may not be able to withstand the pressure increase as the transformer temperature rises.
Many transformers, including high-voltage ones, use the so-called nitrogen protection. With this protection method, the over-oil space of the tank or the oil conservator is taken up by “a nitrogen cushion” consisting of dry nitrogen. This cushion becomes like a barrier that protects the oil against the ingress of other gases and water from the environment. But it is not able to prevent the water and gases that occur inside the transformer from getting into the oil. If necessary, transformer oil nitrogenation is carried out after degassing.
Transformer oil drying during operation is ensured by thermosyphon and adsorption filters. These are devices filled with a sorbent (more often with silica gel). The sorbent absorbs water as the oil circulates through the filter. A thermosyphon filter is installed on the transformer tank, and an adsorption filter is installed on a separate pedestal near the transformer.
But whatever protection systems are used, gas removal and water removal must be ensured before filling the transformer with oil. It is an important part of transformer maintenance. Transformer oil degassing before filling and during operation makes it possible to decelerate the oxidation processes and to enhance the insulation system reliability.
How is thermal vacuum drying of oil performed?
There are several ways to remove water from oil. But zeolite drying and thermal vacuum drying are the most commonly used. Zeolite drying ensures good water removal and raises the oil voltage from 10–15 to 60–70 kV per pass. But after saturation, zeolite requires reactivation. Therefore, if we speak about drying along with degassing, then thermal vacuum processing is more preferable. This type of processing uses the principle of earlier water boiling under vacuum conditions. The most vivid example of this principle can be observed in high altitude environments where water requires the temperature of less than 100 °C to boil.
In thermal vacuum processing, oil is first heated to the temperature of 50–55 °C and then fed into a vacuum chamber. A deep vacuum is maintained inside the vacuum chamber due to the vacuum system operation. The oil enters activator filters and flows out on the inside thereof as a thin film from the surface of which water and gases are intensively released when driven by vacuum.
Thus, thermal vacuum processing allows drying and degassing the transformer oils simultaneously without formation of any waste requiring reactivation, storage, or disposal.
GlobeCore equipment for drying and degassing of oils
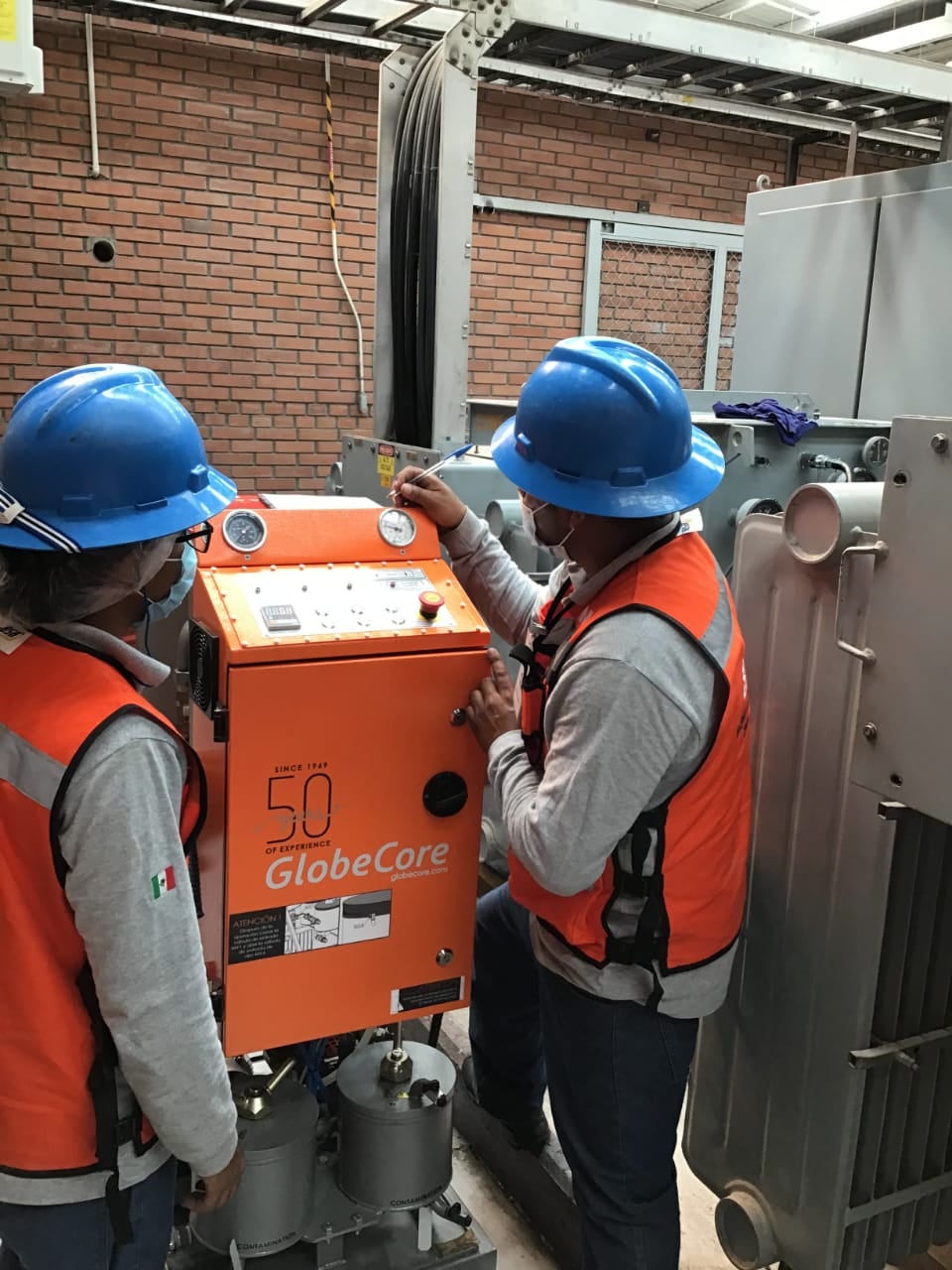
GlobeCore produces CMM units for thermal vacuum drying and degassing of transformer oils.
CMM oil degassing unit performs several functions:
- oil degassing;
- oil dehydration (drying);
- oil filtration;
- transformer vacuumizing;
- filling a transformer with oil under vacuum;
- transformer oil nitrogenation.
Transformer oil characteristics after processing in GlobeCore units:
- breakdown voltage – not less than 70 kV;
- volume gas content – not more than 0.1%
- weight moisture content – not more than 10 grams per ton.
The equipment range includes units with the oil processing capacity of 1 to 15 cubic meters per hour.
Field operation is an important factor in maintenance of transformers. In order to implement this possibility, we mounted the equipment on a trailer equipped with a hitch. Therefore, the unit is quickly transported to a transformer operation site by service team vehicle.
Furthermore, GlobeCore unit can be connected to a transformer and perform oil processing without draining the oil from the tank due to continuous oil circulation in a closed loop. Oil processing can be carried out on both disconnected and operating transformer. In the second case, CMM units are connected to the transformer through TSS (Transformer Security System). This system monitors the oil level in the transformer tank, and when the level drops, for example, due to the presence of leaks, it “isolates” the unit from the transformer. The transformer is always protected, and it is not necessary to disconnect it from power for the duration of oil purification.
What types of oil can be processed by GlobeCore units?
GlobeCore equipment is multifunctional in terms of the types of processed oil. Using CMM units, the following procedures can be performed:
- transformer oil drying and transformer oil degassing;
- hydraulic oil drying and hydraulic oil degassing;
- turbine oil drying and turbine oil degassing;
- industrial oil drying and industrial oil degassing.
It is difficult to cover all aspects of transformer oil drying and degassing within one article; thus, you will probably have questions. Answers to them can be obtained using some of the contact details available in the appropriate section of our website.