PPM Inline Oil Heater. Stream oil heating
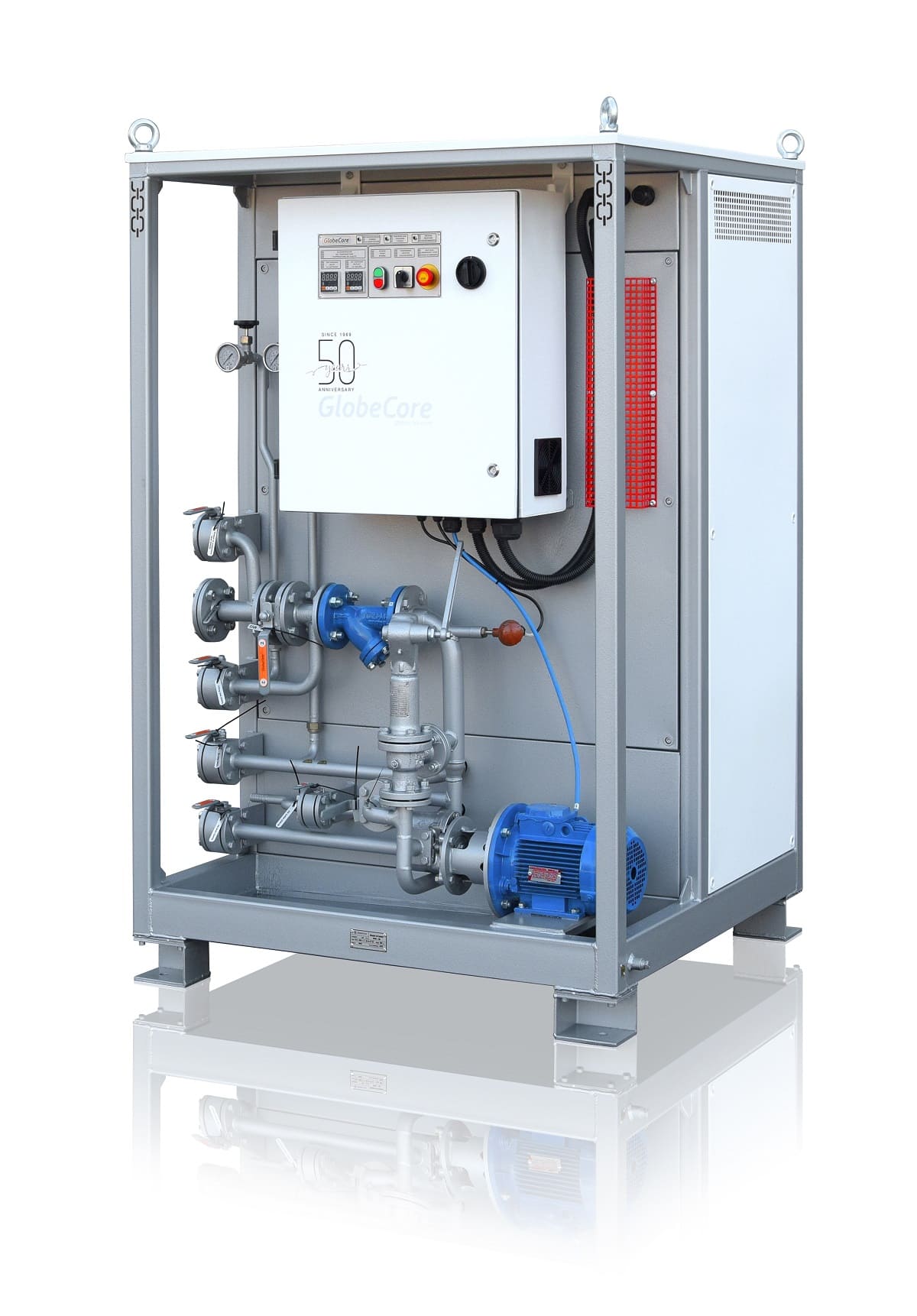
PPM
-
Advantages
- Small and compact heating units that can be easily transported to the place of use;
- Low heating power consumption;
- No overheating. After switching the unit off, the oil temperature may rise by 15-20 degrees.
- Easy to maintain.
The PPM oil heating1Oil heating is used for treatment of oil in degassing, drying and regeneration machines to accelerate the process. Dehydration is based on the difference of water and oil boiling points. Since water boiling point is lower, heating can evaporate that water from the oil before the boiling point of oil is achieved. unit is designed for the heating of transformer oil2Transformer oil is an oil that is stable at high temperatures and has excellent electrical insulating properties. when: (1) adding oil to transformers; (2) replacing transformer oil; and (3) when drying transformers3The drying process should be carried out to remove water and air vacuoles contained in the cellulose-based paper of transformer.. Additionally, the unit can heat mineral oils4Mineral oil is any of various colorless, odorless, light mixtures of higher alkanes from a mineral source, particularly a distillate of petroleum., industrial oils, turbine oils5Turbine Oil – any oil used to lubricate the bearings and auxiliary machinery in steam and hydraulic turbines, in turbopumps, and in air, gas, and refrigeration turbocompressors. Turbine oils are also used as lubricants and working fluids in various types of closed-cycle industrial machinery. and other types of oils as well as non-corrosive liquids.
This oil heating unit is best suited for power plants, oil handling facilities, and facilities that perform transformer repairs and maintenance. The unit can be operated either indoors or outdoors under a suitable canopy.
The abovementioned oils and liquids should have less than 70 cSt kinematic viscosity6Absolute viscosity provides a measure of a fluid’s internal resistance to flow. at the temperature of 50°C. The CMM-P is also used for heating of petroleum products in the petroleum refining industry, and can also be used for heating liquids containing sand, sludge, etc.