US-6S Transformer vacuum furnace
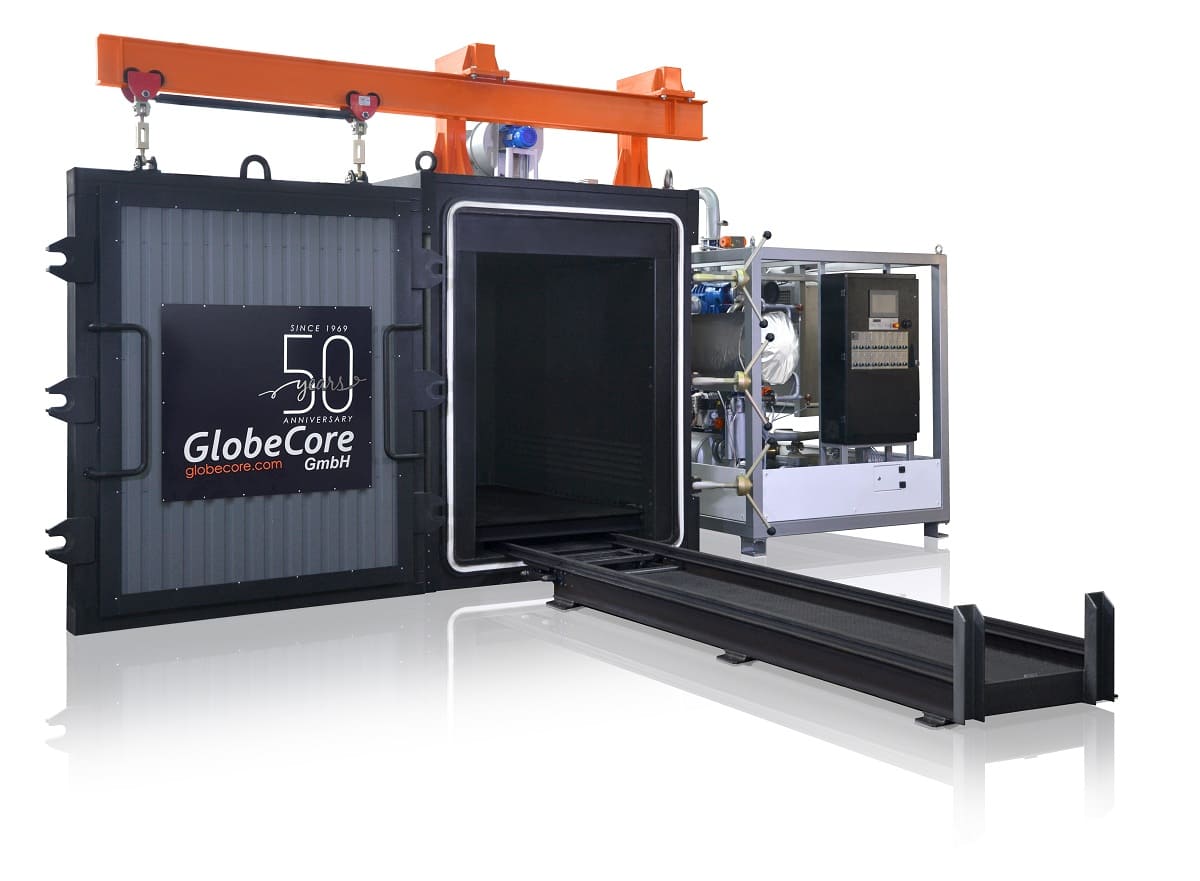
US-6S
-
Advantages
- uniform drying of the entire transformer core volume;
- economic use of electricity;
- reduced duration of drying;
- simple operation;
- removal of moisture from chamber.
We present to your attention a transformer vacuum1Vacuum is space devoid of matter. An approximation to such vacuum is a region with a gaseous pressure much less than atmospheric pressure. furnace US-6S, designed for drying the solid insulation2 The solid insulation materials widely used in the transformer are paper, pressboard, and transformer board, which are formed from the cellulose found in plants. of power transformers3A transformer is a static electrical device that transfers electrical energy between two or more circuits..
A common practice during the production or repair of power transformers is to remove moisture from paper insulation. The dried insulation has dielectric strength4Dielectric strength is the minimum applied electric field (i.e. the applied voltage divided by electrode separation distance) that results in breakdown. This is the concept of breakdown voltage. 20 times greater than not dried one, as moisture affects its dielectric breakdown5Electrical breakdown or dielectric breakdown is when current flows through an electrical insulator when the voltage applied across it exceeds the breakdown voltage..
Depending on the types of transformers there are several ways to remove moisture from the active part. One of them is drying with a vacuum furnace (vacuum oven).
Drying of power transformers6The drying process should be carried out to remove water and air vacuoles contained in the cellulose-based paper of transformer. with a vacuum furnaces has the following advantages:
- more intensive evaporation of moisture in comparison with drying with warm air or natural drying;
- optimal overall performance and reduced processing time.
GlobeCore offers a transformer vacuum furnace with modifications, adapted to meet specific needs of the customer. The design, accounts for productivity, dimensions, and placement location, loading method, degree of automation, etc.
The following picture shows a vacuum drying cabinet US-6S.
Transformer vacuum furnace: the main components and assemblies
1 – Control cabinet
2 – Vacuum unit BV-1000
3 – Compressor
4 – Oil heater PPM-18
5 – Vapor condenser
6 – Condensate collection tank
7 – Furnace chamber
8 – Door of the furnace chamber
9 – Sliding carriage
Principle of operation
The active part of the transformer is loaded onto the sliding carriage by a travelling crane or a loader. The control of the carriage movement (motorized drive), closing and opening of the doors of the furnace chamber (pneumatic drive) is performed by an operator from the control cabinet.
To heating of the furnace chamber is done by technical oil, which, in turn, is brought to the required temperature by an oil flow through heater.
Remember that the price for a transformer vacuum furnace depends on the required dimensions, capacity, and technological features of the customer’s process.
Additional Features
Also, GlobeCore produces vacuum drying chambers for various raw materials:
- powders and pastes;
- food products;
- wood, etc.