In this article, we will look at transformer oil degassing, how to find out when it is time to degass the oil, what the methods of transformer oxidation protection are and will look at equipment used to remove gases from electrical insulating fluids.
How gases enter transformer oil
Even under normal circumstances, transformer oil can absorb large amounts of gas. Notably, the composition of atmospheric air and the air solved in the oil are different. Atmospheric air consists of 78% nitrogen and 21% oxygen (by volume), while the air in the oil contains 69.8% nitrogen and 30.2% oxygen. The solubility of gases in oil is influenced by temperature and electromagnetic fields.
The main source of gases solved in the oil is the atmosphere. Gas bubbles may also form due to vibration of solid bodies in the oil.
The danger of gases in transformer oil
Most adverse effects caused by gas in transformer oil are due to the presence of oxygen. It causes oxidation of the insulation fluid, which reduces its dielectric performance and has an adverse effect on the entire insulation system of the transformer. The process of oxidation may be started either by atmospheric air or by air dissolved in the oil.
Transformer oil degassing is a process that allows to improve transformer operation reliability and protect the equipment from oxidation.
Methods of oxidation protection
Preventive measures involve protecting the oil from oxygen during transformer operation. These include:
- extra sealing of the equipment;
- using antioxidant additives;
- nitrogen blankets.
A nitrogen blanket effectively replaces air and its oxygen with nitrogen. There are several designs for nitrogen protection. The simplest one is sealing the transformer and filling the empty space above the oil with nitrogen. In practical calculations, the recommended amount of nitrogen is 15% of the total oil volume in the transformer. The nitrogen blanket covers the oil and protects it against contact with with.
Oil expands and contracts with temperature changes, which changes the pressure of gas inside the tank. Large pressure changes may cause problems, so the nitrogen protection system is equipped with a breather valve, which may release nitrogen or let the air in depending on the conditions.
Transformer oil degassing can be performed after analyzing oil samples. It requires specialized equipment. Degassing is the process of extraction of gases from the oil and reducing their content to below regulated standards. This process is performed both on oil already in operation in a transformer, and on fresh oil, which can absorb gases during transportation or storage before dilling the transformer.
The process of transformer oil degassing
Modern transformer oil degassing technologies involve elevated temperatures and vacuum, created by a vacuum pump. Other important parts of the transformer are metal vessels, special fillers to spread the processed oil in a thin film, such as Raschig rings, oil spraying nozzles etc.
It is important to make the oil layer as thin as possible with the largest possible surface area. Flat plates can also be used beside Raschig rings.
There are other known methods of fine oil dispersion, such as Kӧrting nozzles and ultrasonic nozzles.
Transformer oil degassing equipment
Considering the fact the transformer oil is also contaminated by other impurities beside gases (such as solid particles and water), GlobeCore has developed the CMM product range. This equipment facilitates complete oil purification, including oil degassing.
The most important features of the GlobeCore units are:
- wide capacity range (from 160 gallons per hour);
- the capability to process oil inside transformer tank (using the TSS – Transformer Safety System);
- high degree of process automation;
- mobility (equipment can be equipped with wheels or installed on trailers);
- reliable fault protection;
- simple operation and servicing.
Some of the CMM transformer oil degassing units can also perform other function, such as heating oil before putting it into electrical equipment, heating of electrical equipment with hot transformer oil, evacuation and vacuum drying of transformer etc.
If the content of gas in the processed oil is below 10.5%, and moisture content is below 100 ppm, one pass of the oil through the unit raises the oil’s dielectric strength to at least 60 kV and improves purity to -/14/12 (ISO 4406).
Several options are available for the customer to choose from, adding to the standard design of the transformer oil degassing units. Some of the options available are:
- remote monitoring of the unit via mobile phones;
- capacity adjustment;
- intrinsically safe design (ex-proof);
- moisture sensors and particles counters;
- insulation for extreme climates;
- stainless steel construction etc.
A more detailed description of some CMM units:CMM-0.6: a 160 gallon per hour transformer oil degassing and purification unit. This is an ideal choice for treatment of oil used in power transformer, reactors, switches and tap changers.
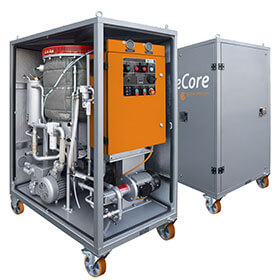
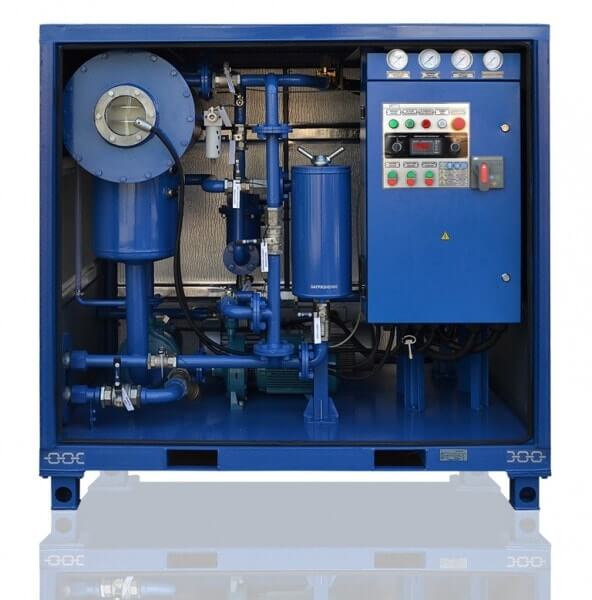