USB-3 Continuous Bitumen Modification Unit (12 m3/hour)
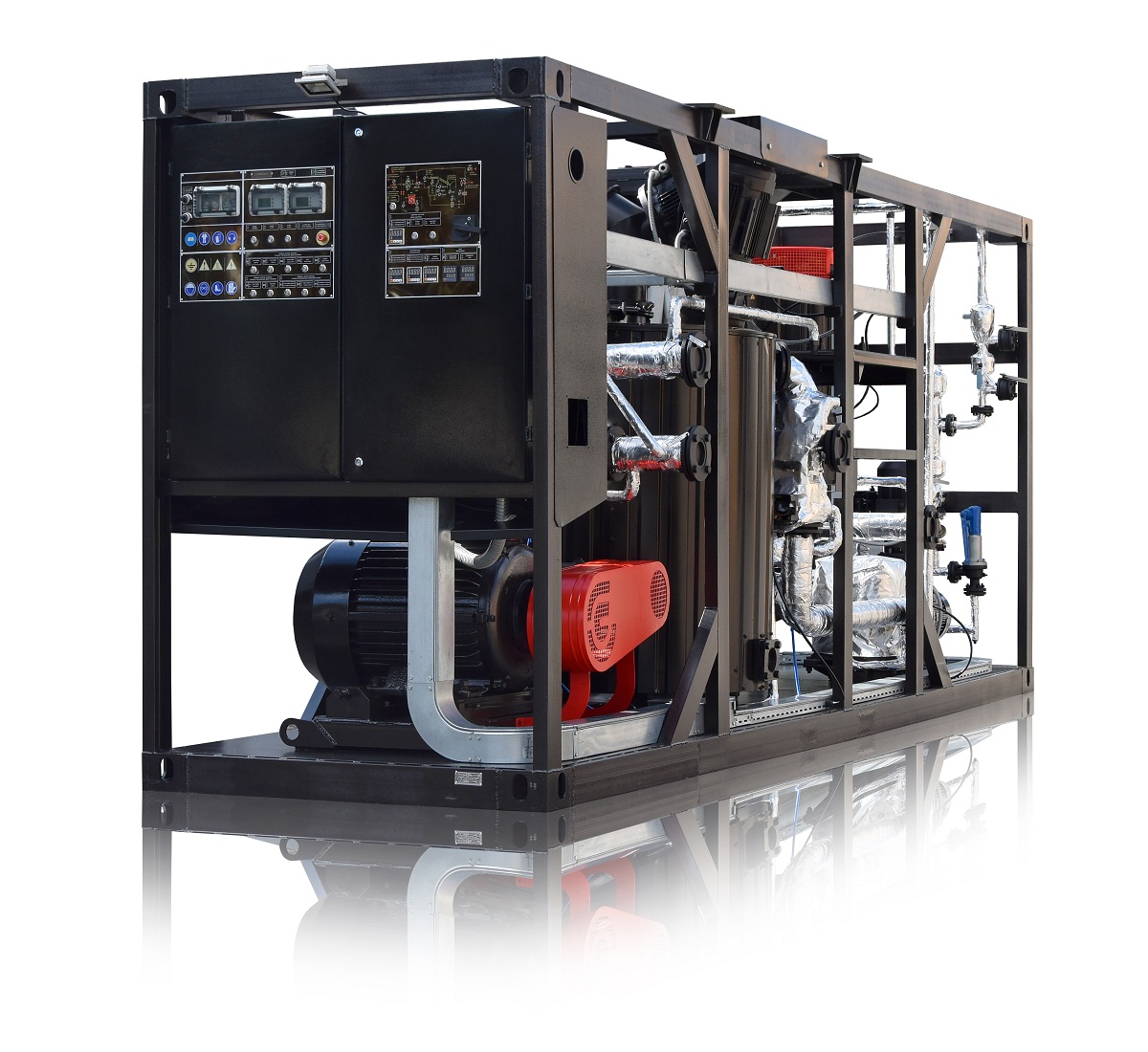
USB-3
-
Advantages
- continuous operation;
- use of any modifiers which can be fed in the form of granules, powder, or liquid;
- possibility to make products in any quantity and in various concentrations of additives;
- high quality of the product made with little time consumed;
- ease of operation and maintenance;
- compactness – the unit is transported in a standard twenty-foot container;
- implemented system for heating with thermal oil;
- modern control system
USB-3 unit is designed for continuous production of modified bitumen (continuous operation unit). The rated capacity of the unit is 12 cubic meters per hour.
When preparing modified bitumen, USB-3 unit allows using any modifiers known as of today, including crumb rubber and various special additives along with all known SBS-polymers which can be fed in the form of granules, powder, and liquid.
The unit makes it possible to implement new formulations of modified bitumen which involve adhesion additives and plasticizers.
The unit can be optionally completed with the following components:
- sulfur feeder;
- polyphosphoric acid feeder;
- Big-bag monorail hoist;
- weighing batcher;
- compressor;
the mill can be completed with a mechanical seal including a support system.
Principle of operation
Figure 1 — Design of USB-3 unit
- Polymer is fed into the hopper.
- The operator sets the polymer modified bitumen formulation (percentage of polymer and additives in bitumen) on the control cabinet.
- The unit is started.
- Bitumen is fed and batched into the intermediate tank. Polymer is fed and batched into the same tank.
- Liquid additives (plasticizers, adhesion additives, etc.) are preliminarily fed and batched into bitumen.
- A high-speed mixer inside the tank preliminarily mixes polymer and bitumen.
- A gear pump supplies this mixture to the mill where polymer modified bitumen (PMB) is ground and homogenized.
- Upon completion of operation, the unit automatically flushes itself with clean bitumen (to avoid the formation of plugs in assemblies and pipelines).
- The unit is ready to be engaged at any time thereafter.
Technical features
- USB-3 unit is installed inside a spatial structure the dimensions of which allow transporting the equipment in a standard 20-foot container.
- The spatial framed structure of increased rigidity makes it possible to quickly assemble and disassemble the unit in the field which is very important when changing the location of an asphalt and concrete factory.
- USB-3 is equipped with a high-speed colloid mill the cutters of which have a special profile allowing to grind, cut, and homogenize polymer-containing bitumen, as well as to obtain a finished product of excellent quality in a single run.
- The mill cutters have a symmetric profile allowing to double their service life. It is just required to change the rotation direction. Furthermore, the mill allows changing the gap between the cutters from 0.1 to 1 mm (depending on the tasks).
- The pumping equipment of the unit is completed with a frequency converter which allows the premixed bitumen and polymer to be supplied to the mill at a specified capacity. Therefore, the mill is relieved of suction and discharge functions and the entire power is spent on homogenizing the product only.
- A polymer batching system is a hopper equipped with a spiral conveyor the drive of which contains a frequency controller. The input polymer (either from regular bags or from Big-bags) is fed from the hopper into the intermediate tank through the spiral conveyor in accordance with the percentage ratio to bitumen which is set by the operator on the control panel.
- An intermediate tank is designed for preliminary mixing of polymer with bitumen and increases the bitumen-polymer contact time which will allow unloading the mill. The intermediate tank is equipped with a high-speed mixer which ensures uniform mixing of bitumen and polymer.
- Liquid additives such as plasticizers and adhesion additives are supplied by self-priming, gear-type, and dosing pumps; the percentage in PMB is set and adjusted by the operator from the central control panel. Each pump of the kind has its own mixer and blends additives into bitumen in front of the intermediate tank and the mill.
- The unit is completed with electro-pneumatic valves, and compressed air can be supplied thereto from a compressor installed on the unit (optional); it allows the unit to be independent on an external source of compressed air.
All the bitumen pipelines, pumps, the mill, and the intermediate tank are heated with thermal oil. Heating with thermal oil is the “mildest” and most efficient heating of assemblies and bitumen lines.
Bituminous grouts — field of application
- Bituminous grouts are classified both by fields of application and by methods of use (cold and hot coating).
- Some grouts require preliminary surface preparation with primers. A primer is a bituminous priming material containing a bitumen and a solvent and having a high penetrability and a short drying time.
- Types of grouts and their uses:
а) Coating grout (cold application):
- waterproofing of surfaces;
- treatment of joints and cracks;
- puttying of surfaces;
- attaching of rolled bitumen materials;
- anticorrosive protection of metal structures.
- b) Coating grout (cold application). It can be used at sub-zero ambient temperatures. It is used for repair and forms an ultrastrong waterproof coating on the steel, concrete, and wood structures sunk deeper into the ground.
с) Bituminous-rubber grout (cold application) is used for waterproofing of foundations, walls, tanks, pipelines, etc.
- d) Adhesive grout (cold application). Designed for attaching the extruded polystyrene to bituminous, bituminous-polymer insulating materials in foundation insulation systems.
Modified bitumen — Fields of application
- Road construction:
- production of asphalt concrete which is used for new construction and repair of first-class roads, bridges, overpasses, road junctions, etc.;
- production of stone matrix asphalt concrete (SMA) for pavement topping of first-class highways and roads;
- production of porous asphalt concrete;
- plaсing of crack-stopping membrane interlayers.
- Hydraulic engineering facilities:
- production of PMB-based grouts for coating of water storage facilities, swimming pools, water supply pipe linings.
- Roofing:
- production of PMB-based rolled roofing materials (Ruberoid, Euroruberoid).
- Bitumen shingles:
- production of grouts for laying and repair of roofing surfaces.