CLM-200.2 Colloid Mill
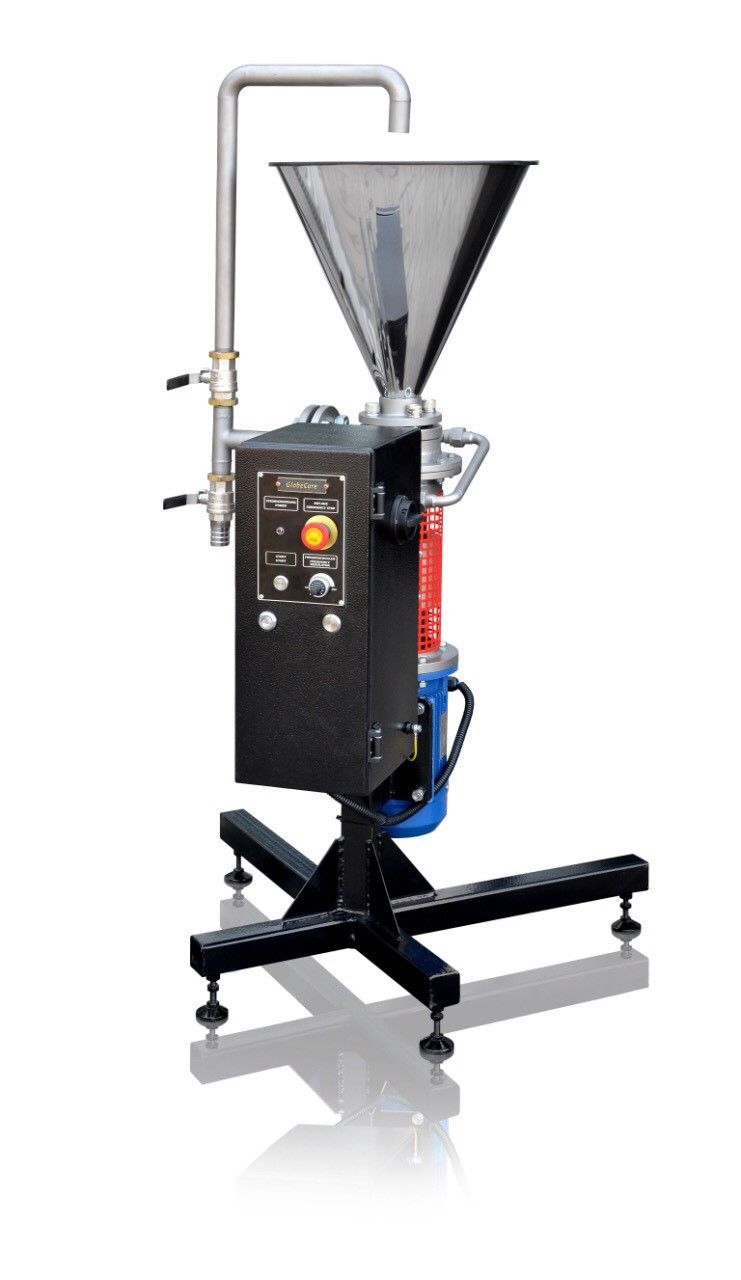
CLM-200.2
-
Advantages
- compact sizes;
- the mill handles various types of products;
- design components of the mill wetted portion are made of stainless, chemical resistant steel;
- the knife axial gap between the rotor and the stator is 0.5 mm, but can be adjusted by changing the number of adjusting shims;
- the drive motor shaft rotation speed is adjusted by means of a frequency converter, and the operating time is set using a timer;
- the mill can be operated both indoors and in sheltered outdoor space.
CLM-200.2 colloid mill is designed for homogenization and emulsification of liquid products in a laboratory environment, as well as for obtaining thick slurries of high shear stresses.
The mill can be used for preparation, dissolution, and processing of many products in various industries.
Principle of operation
The principle of operation of the colloid mill is based on a rotor/stator system diagram. A rotor and a stator consist of concentric tool rings (cutters, knives) with special configurations of grooves and (or) holes that ensure the optimal mode of mechanical impact on processed product.
In working position, the tool rings of the rotor (moving tool) and the stator (stationary tool) enter coaxially against each other and rotate in a contact-free manner at a high relative speed (15…30 m/s). Contact-free rotation is ensured by technological axial and radial gaps.
The processed product enters the operating chamber of the mill housing through the axial bore of the stator (product inlet), is run through the rotor/stator system and discharged in the radial direction (product outlet).
When passing through the rotor/stator system, the product is influenced by complex hydrodynamic processes associated with changes in shear stresses, shear forces, and flow velocity. Chemical reactions occur faster due to increased contact surfaces of chemical agents. As a result, intensive dispersion, emulsification, homogenization, grinding, and pulverization of the processed product are achieved.