CLM-8/16 Colloid mill
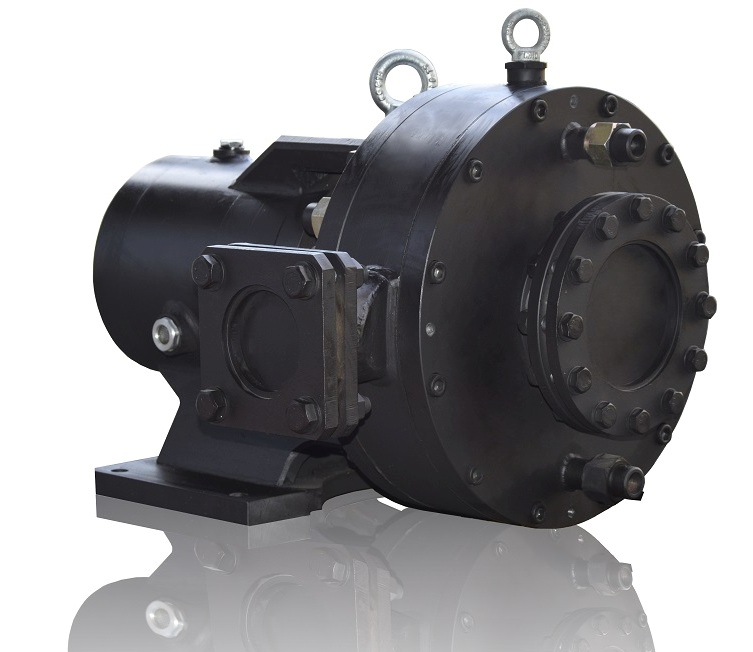
CLM-8/16
-
Advantages
- the mill can be used in various industries;
- depending on the tasks to be performed, the item is supplied with various rotor/stator tooling types and shaft seals;
- the mill wetted portion and components can be made of structural-grade steel, stainless chemical resistant steel, and the steel acceptable for use in the food industry;
- the mill design allows for adjusting the gap between the cutters from 0.2 to 2 mm;
- the mill can be operated both indoors and in sheltered outdoor space.
CLM-8/16 colloid mill is designed for inline homogenization and emulsification of liquid products (thick slurries of high shear stresses).
The mill can be used to prepare, dissolve, and process many products in various industries, in particular, when grinding granulated SBS-polymer applied for modified bitumen preparation.
Principle of operation
The principle of operation of CLM-8/16 colloid mill is based on a rotor/stator system diagram. A rotor and a stator consist of concentric tool rings (cutters, knives) with special configurations of grooves and (or) holes that ensure the optimal mode of mechanical impact on processed product.
In working position, the tool rings of the rotor (moving tool) and the stator (stationary tool) enter coaxially against each other and rotate in a contact-free manner at a high relative speed (up to 47 m/s). Contact-free rotation is ensured by technological axial and radial gaps.
The processed product enters the operating chamber of the mill housing through the axial bore of the stator (product inlet), is run through the rotor/stator system and discharged in the radial direction (product outlet).
When passing through the rotor/stator system, the product is influenced by complex hydrodynamic processes associated with changes in shear stresses, shear forces, and flow velocity. Chemical reactions occur faster due to increased contact surfaces of chemical agents. As a result, intensive dispersion, emulsification, homogenization, grinding, and pulverization of the processed product are achieved.
Bituminous grouts — field of application
- Bituminous grouts are classified both by fields of application and by methods of use (cold and hot coating).
- Some grouts require preliminary surface preparation with primers. A primer is a bituminous priming material containing a bitumen and a solvent and having a high penetrability and a short drying time.
- Types of grouts and their uses:
а) Coating grout (cold application):
- waterproofing of surfaces;
- treatment of joints and cracks;
- puttying of surfaces;
- attaching of rolled bitumen materials;
- anticorrosive protection of metal structures.
- b) Coating grout (cold application). It can be used at sub-zero ambient temperatures. It is used for repair and forms an ultrastrong waterproof coating on the steel, concrete, and wood structures sunk deeper into the ground.
с) Bituminous-rubber grout (cold application) is used for waterproofing of foundations, walls, tanks, pipelines, etc.
- d) Adhesive grout (cold application). Designed for attaching the extruded polystyrene to bituminous, bituminous-polymer insulating materials in foundation insulation systems.
Modified bitumen — Fields of application
- Road construction:
- production of asphalt concrete which is used for new construction and repair of first-class roads, bridges, overpasses, road junctions, etc.;
- production of stone matrix asphalt concrete (SMA) for pavement topping of first-class highways and roads;
- production of porous asphalt concrete;
- plaсing of crack-stopping membrane interlayers.
- Hydraulic engineering facilities:
- production of PMB-based grouts for coating of water storage facilities, swimming pools, water supply pipe linings.
- Roofing:
- production of PMB-based rolled roofing materials (Ruberoid, Euroruberoid).
- Bitumen shingles:
- production of grouts for laying and repair of roofing surfaces.